Mitigating and Managing Moisture in Commercial Concrete Subfloors
Unmanaged moisture can be the biggest enemy for all parts of a flooring system, including the concrete slab.
When it comes to concrete subfloors, unmanaged moisture can mean mold growth, damage to the floor covering installed over it, and more.
But these things are preventable! So let’s go over different concrete moisture management best practices for a concrete slab. We’ll cover:
- Moisture in concrete subfloors
- Moisture management techniques
- The best practice for moisture mitigation
- How Wagner Meters can help
Let’s get started by laying the groundwork (pun intended).
Understanding Moisture in Concrete Subfloors
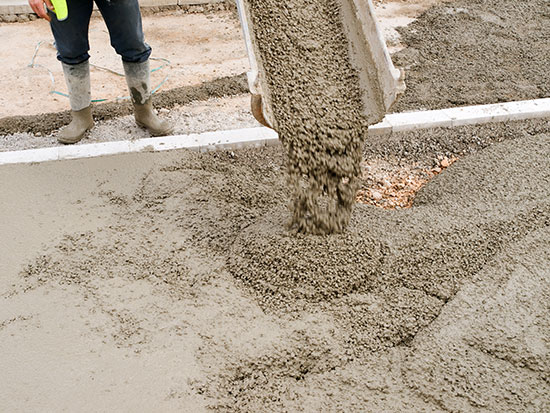
The type of mix you use will impact the moisture condition of your slab.
Moisture in a concrete slab can come from a variety of sources, but most often from the moisture that’s already in the concrete.
When the ingredients of concrete are mixed, water is added. But for the concrete to be considered fully dry, the moisture from deep within the capillaries of the concrete must move up through the slab and evaporate.
This process can take a while: around 30 days per inch of the slab’s depth. And that’s under ideal drying conditions.
However, aside from not enough drying time, excess moisture can also come from other sources. If the vapor retarder is not properly installed, ground moisture can cause issues as it migrates up into the concrete slab. Moisture can also come from poorly directed drainage, leaks, and poor humidity control.
With all these different sources of moisture, it’s no wonder that its measurement and management are key factors in the success of a floor. So here’s what can be done to prevent moisture-related flooring failures.
Techniques for Moisture Management in Concrete Subfloors
Moisture management techniques for concrete subfloors can be broken down into two categories: pre-construction and post-construction.
Pre-construction techniques
Use a better concrete mix
Consider what kind of mix you’re using and how much water goes into it.
The more water used in the initial mix, the more water that must evaporate out of the mix for the slab to dry.
One important note specifically for architects to consider is switching up the aggregate used in the concrete mixture. You can shorten drying time by replacing any lightweight aggregates with lightweight synthetic particles, like polymer beads.
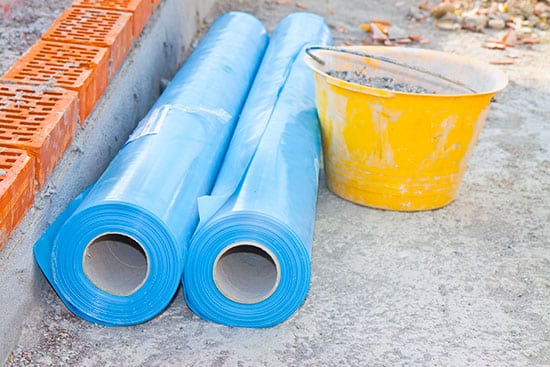
A vapor retarder might simply be a plastic sheet.
Use a vapor retarder
Without a vapor retarder, your slab will probably never dry out.
Before pouring the concrete, prep for the installation by installing a vapor retarder. This can be something as simple as a plastic sheet.
This creates a barrier that allows the concrete to dry without any chance of moisture seepage from below.
Prep the installation area
Preparing the floor covering installation location is just as important as pouring the concrete slab itself. If the space isn’t prepared, the concrete drying time will be much longer than it might need to be.
Here are some important things to keep in mind:
- Make sure the space is enclosed. This protects the slab from the elements.
- Ensure that all the “wet” construction elements are completed, such as priming and painting the walls.
- Have the HVAC system installed and running. Controlling the temperature and humidity in that space means the slab can dry optimally without any interference from the environment.
Post-construction techniques
Apply a moisture mitigation system
A moisture mitigation system goes on top of the concrete surface and prevents moisture from permeating into the flooring installed above it.
Though expensive, this can indeed be a viable solution if drying the concrete is not possible. This could apply in situations when you have a limited timeframe to complete the flooring installation and finished flooring products are being installed over the concrete subfloor.
Moisture mitigation systems are normally two-part epoxies. Make sure you use a product from a reputable manufacturer.
Use an extra dehumidifier
You can improve your drying time and manage the moisture in concrete by running an industrial dehumidifier along with a large fan after installation. This decreases the amount of moisture vapor in the air and gives the moisture in the concrete somewhere to go.
No matter which pre- or post-construction techniques you use, let’s look at a key best practice to make sure moisture in your concrete is properly dealt with.
Moisture Management Standard Practice
Vapor retarders and dehumidifiers are considered essential steps in moisture management. But there is one thing that will make all the difference: properly assessing the moisture condition of your slab.
If you aren’t assessing how much moisture is currently in the concrete slab (and not just on the surface), you’re going into the drying process blind.
And the results could be detrimental.
You could unnecessarily extend the timeline, wasting both your time and money (and your client’s time and money). If you move forward with installing the floor when the slab isn’t dry, you risk serious damage to the finished floor covering. Then, you have to remediate both the damage to the floor covering as well as the moisture in the slab.
So the essential question is, How do you accurately assess the moisture condition of your concrete slab?
There are a few options:
- Calcium chloride testing
- Concrete moisture meters
- Relative humidity (RH) testing
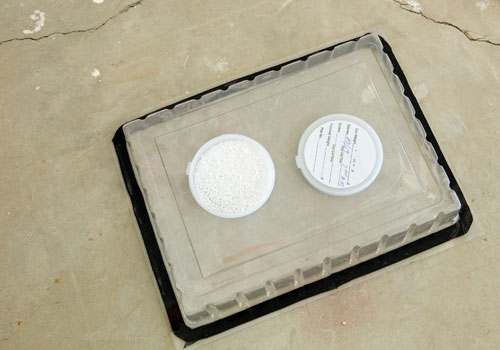
Calcium chloride tests simply don’t give you the information you need to truly understand the moisture condition of your slab.
Calcium chloride testing
Calcium chloride testing really only tests the surface conditions of the slab, which doesn’t give you a full picture of the slab’s moisture condition.
Concrete moisture meters
Concrete moisture meters, such as the C555 from Wagner Meters, are a great option for identifying moisture “hot spots” in the concrete.
Not only does this tell you how much moisture you’re dealing with, but it also helps make each succeeding step of the measurement and mitigation processes easier and more effective.
Once you’ve done your initial moisture condition assessment across the slab, you can now better identify where to place RH testing probes.
There may be some cases when the floor covering manufacturer recognizes the use of a concrete moisture meter as the sole testing method, even though the ASTM F2659 standard requires additional steps. But if you’re using your concrete moisture meter as the sole testing method, you will no doubt want to use the most accurate moisture meter on the market—Wagner Meters’ C555.
Relative humidity (RH) testing
While each of the above assessment methods will give you some kind of answer to work with, only one option will give you a consistently accurate answer: relative humidity testing.
This testing method is the most effective way to measure moisture in concrete, especially when the RH testing is done in situ.
In other words, the measuring should be done within the slab itself via an inserted probe. This fully complies with the guidelines of ASTM F2170.
And if you’re inserting probes into your concrete slab to determine how the rest of the moisture management process will go, you want a relative humidity testing system you can fully rely on.
That’s where Wagner Meters comes in.
Wagner Meters: The Key to Proper Moisture Management
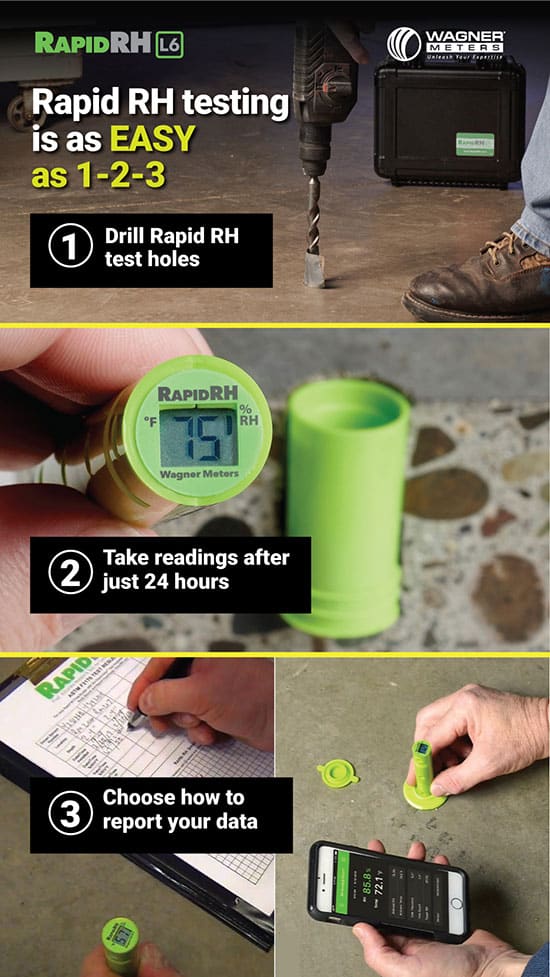
RH system can give you all the information you need to properly assess your concrete slab’s moisture condition.
When you’re preparing a concrete slab for flooring, it’s not just the floor that’s at stake. It’s your reputation. You want to be confident in your moisture management process. You want to be able to provide complete success for your clients’ flooring projects.
Wagner Meters helps you achieve this level of quality and confidence with its revolutionary, easy-to-use, complete RH testing system.
Let’s take a look at what this system entails.
Rapid RH® sensors
These small sensors are the cornerstone of the system, as they provide the last word in the moisture measurement process. You can use them alone for successful RH monitoring in your concrete slab.
These sensors give you accurate RH measurements throughout the slab so you can be continually informed of its moisture condition and track how fast it’s drying.
This means you can give your clients a more reliable timeline, protecting your schedule while also managing their expectations and safeguarding your reputation.
In situ sensors are placed by drilling into the slab and inserting the probe.
Once within the hole, the single-use sensor can remain there and take RH measurements as long as you need to measure them.
To further save you effort, you can also use the RH sensors together with the DataGrabber® loggers. When it’s paired with Wagner’s DataMaster™ smartphone app, all you have to do is walk around the jobsite and approach each sensor; the test data will transfer straight to the app for you to check.
One Wagner customer, Bill Lepito, does hundreds of RH tests a year. He says, “I’ve been using Wagner for eight or nine years. It’s fast, simple and effective.”
Why Not Choose the Most Accurate, User-Friendly Relative Humidity Testing System Available?
You may do everything else right, but if the concrete moisture conditions aren’t properly measured and managed, the integrity of your slab (and anything installed over it) is at stake.
And how can the moisture conditions be properly managed if they’re not properly measured?
When you use Rapid RH in situ sensors, you can rest assured that at any point in the drying process, you’ll know exactly how much moisture remains within the slab. This peace of mind can also extend to the rest of your team and to your clients. They’ll know that your project’s timeline is based on the most accurate data possible.
So if you want to safeguard your success in flooring projects, it makes sense to use the most user-friendly, reliable concrete moisture measurement tools on the market.
Make the Rapid RH system your number-one choice for moisture management!
And you don’t have to stop there. Learn more about our comprehensive moisture management systems.
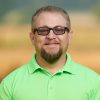
Jason has 20+ years’ experience in sales and sales management in a spectrum of industries and has successfully launched a variety of products to the market, including the original Rapid RH® concrete moisture tests. He currently works with Wagner Meters as our Rapid RH® product sales manager.
Last updated on September 25th, 2024