5 Reasons Moisture Is Coming Up Through Your Concrete Floor
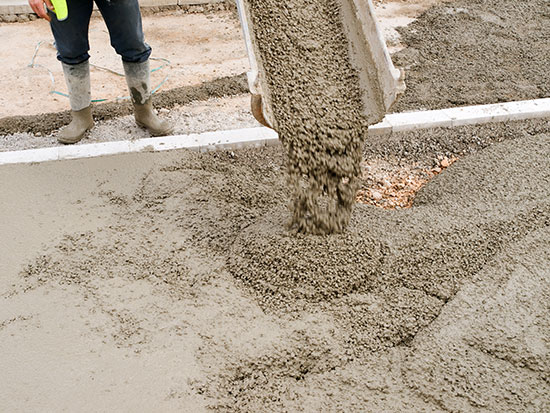
When concrete is first poured, it’ll contain a lot of excess moisture that needs to dry off. Having the right water-cement ratio can prevent this from taking longer than necessary.
You recently installed a hardwood floor, and you made sure to check the wood’s moisture content many times, allowing the wood to acclimate fully before installation.
Now, the floorboard edges are turning upward—a condition called cupping. You know there must be a moisture issue. But how?
It may be coming up from the concrete slab beneath.
But you’re still confused. After all, you used a concrete moisture meter, and the slab seemed dry. Where is all that moisture coming from? We’ll look at five possibilities:
- Too high of a water-cement ratio
- Not enough drying time before installation
- Vapor barrier problems
- Plumbing leaks
- Poor drainage
Once we’ve covered these potential moisture sources, we’ll provide you with some tips and tools for keeping concrete moisture under control.
1. Too High of a Water-Cement Ratio
Moisture is a core component of concrete. It’s a mixture of water, cement, and aggregate materials that form a paste. The water creates a chemical reaction that helps the concrete to harden once it’s been poured.
But just because concrete has hardened—or cured—doesn’t mean it’s dry.
A truckload of concrete contains about 320 gallons of water. That’s a lot of moisture that has to evaporate!1
The moisture dries from the surface first, creating a gradient: more moisture in deeper parts of the slab and less moisture on the surface. You may not notice the excess moisture.
That’s why having the right water-cement ratio from the start can help.
How much water should you put in your concrete truck? A general recommendation is about 45 pounds of water for every 100 pounds of cement—a 0.45 water-cement ratio.2 (However, we advise you to always follow the architect’s specified mix design.)
2. Not Enough Drying Time Before Installation
Regardless of whether or not the water-cement ratio of the concrete was correct, it needs time to dry before a floor can be installed on top. This is because the moisture from deep within the slab slowly migrates to the top and evaporates off the slab.
If the slab hasn’t had enough time for all that moisture to be released, it will continue to release the moisture once the floor has been installed on top.
The best way to know for certain that the concrete has dried enough is to perform in situ relative humidity testing. More on that test later. But first, let’s cover three more reasons for moisture coming into your floor.
3. Vapor Retarder Problems
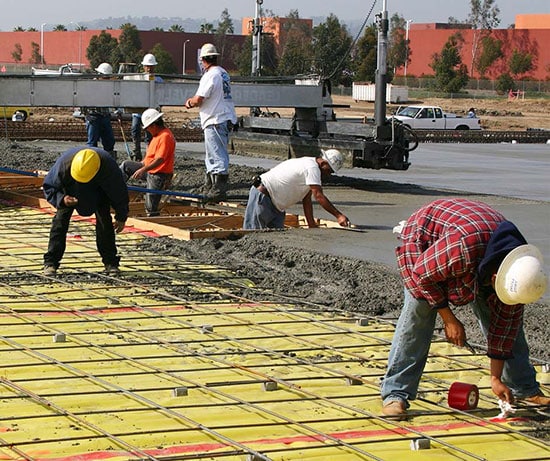
A damaged or improper vapor retarder can result in ground moisture seeping up through the concrete.
A vapor retarder goes beneath the concrete to prevent moisture from coming up into the concrete. Some problems with vapor retarders are:
- Not having one
- Having the wrong kind
- Having a damaged one
ASTM E1745 is the standard for vapor barriers under concrete slabs. It places vapor retarders into three classes (A, B, or C) based on their permeance, tensile strength, and puncture resistance.
When it comes to moisture, permeance is one of the most important factors because it determines how much moisture can pass through the retarder. It’s measured in perms, and the lower the rating, the better. ASTM E1745 requires that all classes of vapor retarders measure at 0.1 perms or less.
Unfortunately, vapor retarders can get damaged during the building process. So, if you can, check that the barriers are intact before putting down concrete. Otherwise, holes or tears could allow moisture in.
4. Poor Drainage
A good moisture retarder will prevent water from coming up from the ground, but without one, poor drainage could become an issue. If the home or building was graded improperly, rain, snow, and sprinklers could cause water run-off to pool around the structure rather than draining away from it.
If water builds up in the soil around the foundation of the building, the pressure from that water—known as hydrostatic pressure—can force moisture through the concrete and into the building.
This typically happens if the water table is higher than the concrete slab, such as with a below-grade basement (in which case you may not want to install a hardwood floor anyway).
5. Plumbing Leaks
Plumbing leaks from above the concrete can cause moisture to seep into it. Sometimes, these leaks in supply or drain lines are hidden, wetting the concrete for weeks or months before anyone notices the problem.
And if left untreated, they could cause significant damage to the home or building.
How to Keep Moisture Under Control
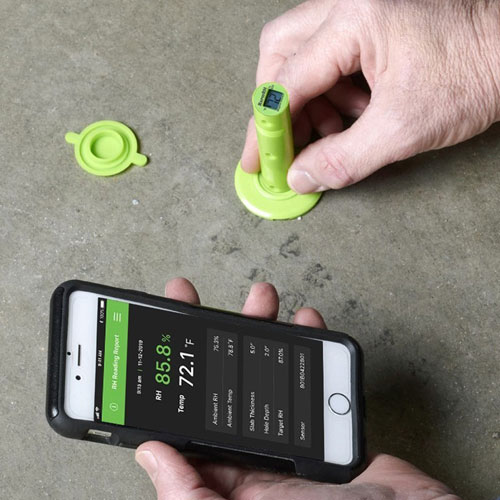
Relative humidity testing of the concrete floor is the first step in keeping moisture under control.
To properly deal with moisture issues in your concrete, you’ll need to measure the amount of moisture in the concrete, assess the situation, and mitigate the problem based on the source of the moisture. Unfortunately, you may have to pull up the hardwood flooring that’s there.
As we mentioned earlier, one of the challenges with concrete slabs is hidden moisture.
Though a concrete moisture meter can help indicate moisture “hotspots,” it doesn’t measure much beyond one-inch deep.
The ASTM F2170 standard recommends using the relative humidity test, which involves drilling down to 40% depth of the concrete when drying from one side. There, you can place probes and get a better overall picture of the concrete’s moisture condition.
Place three probes for the first 1,000 square feet of the slab and one probe for every additional 1,000 square feet. This will ensure adequate testing of the whole slab.
If the relative humidity of the concrete is too high, allow additional drying of the concrete before putting any flooring back.
Depending on the moisture source, you may also need to:
- Fix leaks
- Develop a better drainage system
- Use external sealants
- Install a sump pump
- Install a moisture mitigation system (as a last resort)
Once the slab is dry and you install a floor over it, how can you know a problem won’t arise again?
The best way to have peace of mind is to monitor the moisture conditions of your hardwood floor. You can do this (or empower your customers to do it) with a small data logger, such as Floor Sentry®, that inserts into the underside of a wooden plank.
It’ll immediately alert you if the floor conditions go out of range—and you’ll be able to fix the problem before your hardwood floor gets damaged.
Say Goodbye to Concrete Moisture Problems
Don’t wait to address a concrete moisture problem. It’ll only worsen and cause more damage to the building or property.
Taking steps to diagnose the problem and measure concrete moisture levels will give you a clear path forward for controlling any moisture. What’s more, you can have complete peace of mind with tools that track the ambient conditions of the hardwood floor. Moisture won’t be able to sneak by again.
Learn how Floor Sentry can help you catch sneaky moisture in your hardwood floors.
2. “How to Calculate Water Cement Ratio for Concrete,” ConcreteNetwork.com.
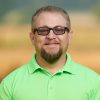
Jason has 20+ years’ experience in sales and sales management in a spectrum of industries and has successfully launched a variety of products to the market, including the original Rapid RH® concrete moisture tests. He currently works with Wagner Meters as our Rapid RH® product sales manager.
Last updated on March 7th, 2025