Osmotic Blisters: The Plague of Resin Floors
Since the 1960s, builders and consumers have selected resin floors for their seamless strength. Base resin, when mixed with reactive hardener, induces in situ polymerisation.
Although builders use different chemicals to manufacture resin floors, this curing reaction is critical to their formation.
High School Chemistry: Osmosis
When builders apply resin floors to concrete with adhesives, bonding adhesives form a partially permeable membrane. Think of the concrete as one slice of bread. The synthetic resin floor covering is the other slice, and adhesive holds the sandwich together. During procurement, moisture flows from the more diluted solution to the more concentrated one – in this case from concrete to resin. That’s as far as theory can safely be applied to resin floors.
The adhesive membranes cause unequal moisture migration. Put simply, the membrane allows safe passage to moisture while denying similar migration to dissolved substances. In essence, moisture saturates one slice of bread at the expense of moisture in the other.
“What Happened?”
Osmotic blisters are a building contractor’s nightmare for two reasons. First (and obviously), they can ruin otherwise good work. Secondly, too many builders install resin floors without knowing the profound influence of moisture on the formation of osmotic blisters. Any time one element passes more freely than another, imbalance ensues.
Apply resin floors to unequilibrated concrete substrate slabs, and you invite the moisture to blister the surface of resin floors. In order to fix them, we must first understand osmotic blisters.
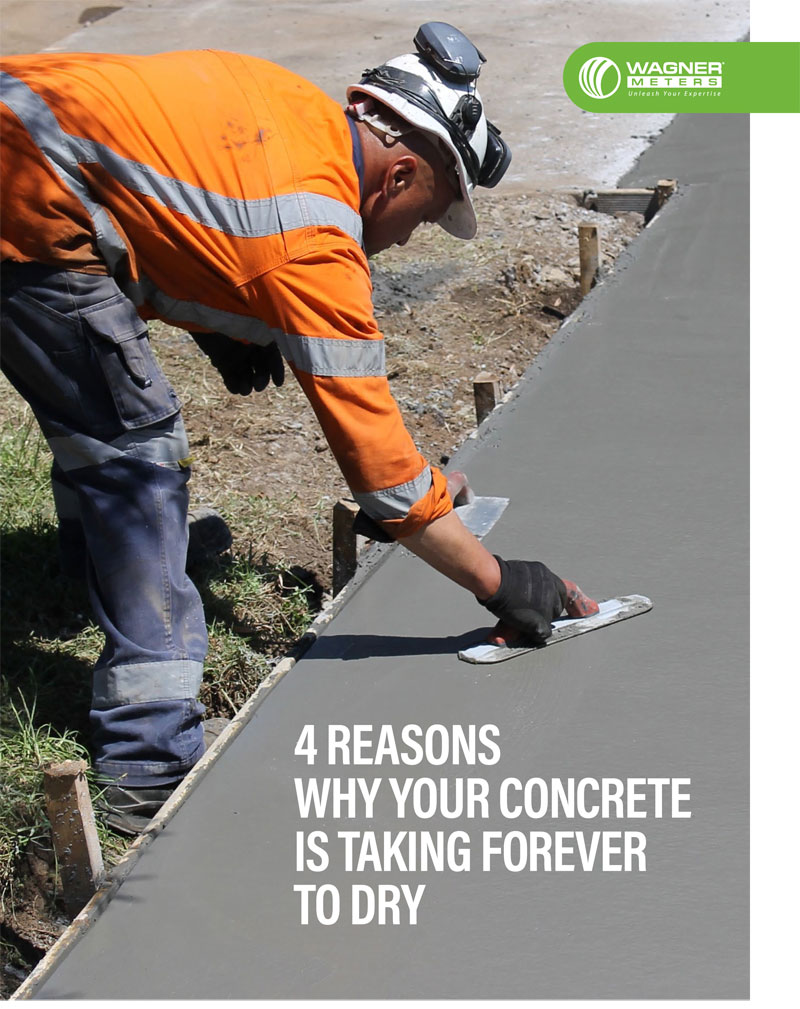
Free Download – 4 Reasons Why Your Concrete Is Taking Forever to Dry
The Ingredients of Osmotic Blisters
- Semi-permeable membrane: in construction, it is often the bond interface or the extreme upper layer of the concrete.
- Concentrated water-soluble material (organic or inorganic): the wild card. This can be traced to anything from the resin ingredients in the epoxy coating or concrete admixtures. Soluble salt content in concrete will do it, too.
- Water: one concrete’s three core ingredients. Moisture always rises from the bottom of the slab to the top to reach compressive strength, concrete’s destination of choice.
The Natural Cure
There is no litmus test for osmotic blisters. However, relative humidity (RH) measurement provides installers with all-important data on concrete readiness. Equilibrated RH levels are reached when the slab’s RH% is “balanced” with that of its surrounding service temperature and RH. If RH is too high, builders must hold off on the installation of resin floors.
Preemptive Measures
- Try to minimize the amount of soluble salts in the concrete mix design.
- Install a water vapor retarder beneath the slab.
- Avoid acid etching as surface preparation for a coating application.
- Check that the epoxy coating resin constituents are accurately proportioned and properly mixed.
- Check the slab’s RH during curing and drying to ensure its readiness.
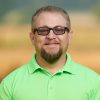
Jason has 20+ years’ experience in sales and sales management in a spectrum of industries and has successfully launched a variety of products to the market, including the original Rapid RH® concrete moisture tests. He currently works with Wagner Meters as our Rapid RH® product sales manager.
Last updated on September 10th, 2024
I’m looking to set up a flooring company. I have 8 years experience but need up to date advise and products.
Terence:
Sounds like an exciting time. Good luck in the adventure. What is it that I can help with specifically?