Improve Your ROI with These Moisture Measurement Tools
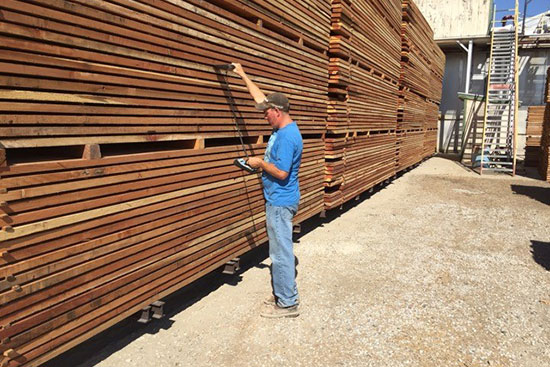
At Siskiyou Forest Products, they’ve found that an industrial handheld meter like the Wagner L622 is great for measuring the MC of large batches of lumber.
How do you cut expenses for your forest products business—all while improving quality and increasing your return on investment (ROI)?
For Carl Diebold Lumber, the right moisture measurement tools have been key.
Producing high-grade boards valued at $4,000 to $5,000 per 1000 board feet, they couldn’t afford to end up with damaged wood. By monitoring the wood’s moisture content as it dried, they were able to prevent damage—and cut energy costs.
To learn their secret, we’ll explore those moisture testing tools in depth. But first, we need to understand why moisture testing matters in this industry.
Why Moisture Testing Is Important for Wood Products Manufacturers
Incorrect moisture content is enemy #1 of wood, causing an estimated 80% of wood products defects. So, it pays to test for moisture and avoid that damage.
Doing so has many benefits for manufacturers:
Improved product quality
Proper moisture testing will help prevent underdrying or overdrying of wood.
If wood dries too much, it can show defects like checks or splits. As a result, you may have to discard the wood or sell it at a lower price.
And if the wood doesn’t dry enough, you may have to send it through the kiln process a second time, losing time and efficiency.
Speaking of efficiency…
Decreased energy costs
Any extra time your wood spends in the kiln costs you money. Even if it doesn’t damage the wood, it’ll hurt your bottom line.
Of course, you want the wood dry enough to prevent downstream defects and meet your customer’s requirements.
But every percent that your wood is dried below that threshold will cost you a minimum of $3 per 1,000 board feet of lumber. And let’s say a company that processes millions of board feet every year is drying their wood 5% below what is needed. Think about how many thousands of dollars per year are being lost in operating costs!
Moisture testing can streamline your process, helping you to dry to the exact percentage you need—and no more!
A good reputation
Let’s say a customer files a wet claim against you because the batch they received from you had too high of a moisture content (MC). What might happen?
They might demand a refund. Or refuse to pay for the wood.
You might lose them as customers, but even worse, your reputation might suffer. After all, what’s to say they won’t tell others that your product quality is unreliable?
But you can avoid all these risks with moisture quality control. The right tools can mean putting out products that consistently meet your customers’ expectations.
So, what are those tools? Let’s find out.
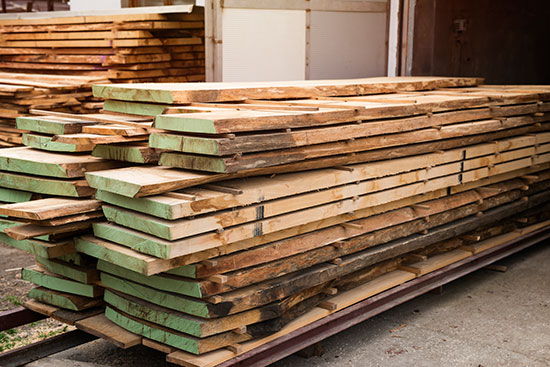
When drying slabs like these in a kiln, you can save energy and ensure that you meet your customer’s requirements by using an in-kiln moisture measurement system.
Industrial Moisture Meters
Industrial moisture meters, like those sold by Wagner Meters, are pinless moisture meters that use an electromagnetic sensor to detect the MC of a piece of wood.
This non-damaging type of meter won’t leave pinholes in the wood the way pin meters do, and it’s a much more efficient way to measure moisture.
The industrial version has a large scanning plate with an ergonomic handle—great for measuring large batches of wood. As you scan the wood, the meter can store over 5,000 readings and send them to PC-based reporting software. No manual recordkeeping necessary!
Wagner’s L622 digital recording moisture meter is a staple at Siskiyou Forest Products, which produces high-end finger-jointed and edge-glued wood materials. For them, an MC under 12% is critical for wood to run through their glue line.
Aaron Duchi, who runs the kilns at Siskiyou Forest Products, appreciates no longer having to use a pin meter or record readings by hand.
He shares:
“[The Wagner meter] not only measures the lumber faster, but it does all the recording work for me. It calculates all the information for each sample I take and sends it to my computer screen so I can quickly print it out.”
But beyond using handheld meters, many businesses invest in large-scale moisture measurement systems, like the one we’ll discuss next.
In-Kiln Systems
An in-kiln moisture measurement system uses electromagnetic wave technology to measure the MC of the wood in a kiln. Each kiln unit has four to eight sending units with moisture-sensing zones. These zones connect to user interface software on a computer, allowing the kiln operator to monitor the MC of the wood in each zone.
With this real-time view of the wood’s MC and drying trends, the kiln operator can track progress and stop the kiln as soon as the wood has reached the desired MC.
No overdrying and no wasted energy costs!
And that brings us back to Carl Diebold Lumber, which processes about 1.4 million board feet of wood each month.
By using an in-kiln system, they can be sure of meeting their customers’ requirements. They’ve even been able to shorten their drying times by a couple of days because they don’t have to guess when the wood is ready.
And rather than performing many manual checks, the in-kiln system allows them to keep the kilns running while keeping an eye on progress. This saves the energy costs of shutting down the kiln and heating it again.
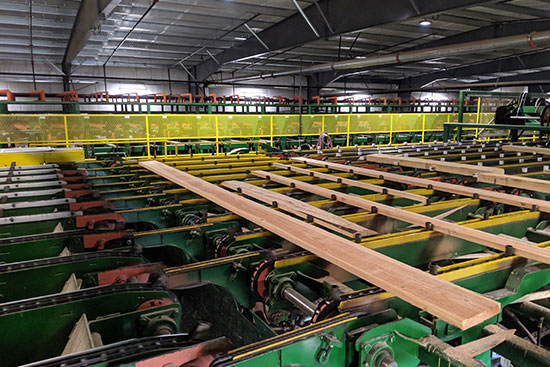
You’ll gain a reputation for top-of-the-line wood products and improve your ROI by using reliable tools for measuring moisture.
In-Line Systems
In-line moisture measurement systems usually sit at the beginning or end of planing or moulding operations. They scan every board, collecting data about the MC of each batch of wood and helping troubleshoot kiln performance. They can also identify moisture spots in the wood that can be trimmed out.
Wagner Meters offers in-line systems in two different configurations: end-to-end and sideways.
End-to-end systems are often on the outfeed side of planers and moulders and measure the moisture in the length of a piece of lumber. They are good for identifying spots with higher MC.
Sideways or transverse systems have sensors that the wood moves over sideways. There are up to eight sensors, which can trigger a mark on wood with moisture issues.
For Manke Lumber Company, using an in-line system has allowed their business to compete in the export market.
A lumber processing and treatment plant in Washington state, they’ve used the in-line system to help them meet Japan’s stringent requirements for housing lumber.
“Everything we do is based off of what the Wagner equipment tells us,” says Craig McNeil, the treating engineer there.
The result?
“We’re able to do a good job because of it. Our report is that our lumber is one of the best they have in Japan.”
What Could Moisture Measurement Tools Do for Your Business?
What if moisture measurement could save you thousands of dollars, improve your ROI, and give you a reputation for top-of-the-line products?
With the right moisture measurement tools, those scenarios are within your reach.
Kerry Cogburn, kiln supervisor for Teal-Jones, a lumber manufacturer in Oklahoma, didn’t hesitate to say that an in-kiln system saves him about $300,000 per year in time, energy costs, and wood-drying efforts. What could your business do with that kind of savings?
Previously published in Canadian Forest Industries
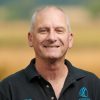
As Sales Manager for Wagner Meters, Ron has more than 35 years of experience with instrumentation and measurement systems in different industries. In previous positions, he has served as Regional Sales Manager, Product and Projects Manager, and Sales Manager for manufacturers involved in measurement instrumentation.
Last updated on March 12th, 2025