Wood Production: Manufacturing & Kiln Drying
In every wooden furniture piece or structure, there’s a story of transformation. A journey from dense forests, where the whispers of leaves and the songs of birds dominate, to bustling lumber mills, where machines hum, and craftsmen work.
At the heart of this transformation is a meticulous process that balances nature with technology, ensuring that the wood retains its innate beauty and meets the diverse demands of modern applications.
This article unveils the intricate processes of wood production, emphasizing the importance of moisture content in ensuring the quality of the final product.
Dive into the world of lumber mills, kiln drying, and the nuanced steps that take wood from tree to polished timber.
- The Lumber Manufacturing Process Generally Follows These Steps
- Kiln Drying Wood for Maximum Value and Usability
- Environmental Impact & Sustainability in Wood Production
Lumber mills turn trees into manufactured wood products. Throughout the process, the moisture content (MC) of the wood is an important factor for producer and end user alike.
The Lumber Manufacturing Process Generally Follows These Steps
- Head Rig: The primary saw cuts the tree into sawn pieces or boards.
- Edging: Removes irregular edges and defects from sawn pieces or boards.
- Trimming: The trimmer squares off the ends of lumber into uniform pieces.
- Rough Lumber Sorting: Pieces are separated based on dimension and final product production, whether the finished piece will be unseasoned (known as “green”) or dry.
- Stickering: Lumber destined for kiln drying production is stacked with spacers (known as stickers) that allow air to circulate within the stack (green product skips this stage and the next).
- Drying: Kiln drying wood speeds up the natural evaporation of the wood’s MC in a controlled environment.
- Planing: Smoothes the wood’s surfaces and ensures that each piece has a uniform width and thickness.
- Grading: Assigns a “grade” to each piece of lumber that indicates its quality level, based on a variety of characteristics, including its MC.
Kiln Drying Wood for Maximum Value and Usability
In order to maximize wood’s value and strength, mills invest both time and money in the kiln drying processes to remove excess moisture from the lumber stack.
In fact, kiln drying on some hardwood species can take up to (and beyond) a month, depending on the initial MC of the wood.
Properly dried wood has many advantages over green wood for both producers and consumers alike. It reduces waste in manufacturing and extends the service life and usefulness of wood products, giving the consumer a stable product that will last for years.
The kiln drying process can vary considerably, depending on the species and initial MC of the wood. In general, however, these are the steps in the process:
- Lumber producers carefully stack “green” wood, using spacers or “stickers” to create gaps for air to freely circulate throughout the stack.
- Once the wood is placed in the kiln, depending upon wood species, the kiln is heated to temperatures between 110 to 180 degrees (Fahrenheit) for conventional-temperature kilns and 230 to 280 degrees (Fahrenheit) for high-temperature kilns.
- Operators constantly monitor kiln temperatures and relative humidity (RH), as well as the lumber’s MC. The goal is dry the lumber to the correct MC for how it will be used.
The profitability of lumber manufacturing depends on the mill’s ability to maximize the wood’s quality throughout the entire lumber manufacturing process.
If the wood in a mill’s production line is too wet or too dry, the finished product may receive a lower grade and will have a lower dollar value than a piece that has been properly kiln dried.
For the post-drying lumber processing, in-line moisture content measurement systems can easily identify and mark pieces that are either too wet or too dry.
These pieces can then be pulled from the production line before further processing and possibly be re-dried or re-milled as necessary to create the highest grade lumber or wood component possible for that piece, thus increasing the mill’s profits and giving consumers access to better quality materials.
Many consumers and builders believe that concerns about the lumber MC end when the wood is shipped out of the mill. In fact, wood products should be constantly measured and monitored to assure that the MC levels are at optimum EMCs. Wood will naturally continue to gain or lose moisture until it reaches this EMC balance with the surrounding environment.
Environmental Impact & Sustainability in Wood Production
The modern world is increasingly conscious of the environmental footprint we leave behind. The wood production industry, traditionally seen as a major consumer of natural resources, is undergoing significant shifts in its approach to sustainability and environmental responsibility.
Here are three:
1. The Importance of Sustainable Forestry
Sustainable forestry refers to managing forests to ensure that they continue to provide the timber resources we need and other ecosystem services, such as clean water, wildlife habitat, and carbon sequestration.
It’s a dynamic and evolving approach, aiming to balance our current needs and those of future generations.
Key principles include:
- Selective Logging: Only certain trees that have fallen, allowing younger trees to mature and ensuring the forest can regenerate.
- Reforestation: After logging, new trees are planted or naturally regenerated to replace those cut down.
- Biodiversity Conservation: Sustainable forestry practices prioritize the conservation of native species and habitats, ensuring that the forest ecosystem remains healthy and diverse.
2. Modern Mills Reducing Carbon Footprint
The timber industry has historically been a significant carbon emitter. Still, with technological advancements and a shift in mindset, many modern mills are pioneering practices to reduce their carbon emissions.
- Energy Efficiency: Many mills are investing in energy-efficient machinery, reducing their electricity usage.
- Waste Reduction: Sawdust and offcuts, once seen as waste, are now being used to produce biofuels and other products, ensuring fewer materials end up in landfills.
- Carbon Sequestration: By maintaining healthy forests, mills can benefit from trees’ natural carbon storage capabilities, effectively offsetting some of their emissions.
3. Benefits of Using Reclaimed Wood in Production
Reclaimed wood, salvaged from old buildings, barns, and other structures, is gaining popularity in modern construction and furniture making due to its aesthetic appeal and environmental benefits.
- Waste Reduction: By reusing timber from old structures, we reduce the demand for new wood and prevent valuable materials from ending up in landfills.
- Character and History: Reclaimed wood often has a rich history, unique textures, and patterns that new wood doesn’t offer. This makes it a popular choice for crafting unique, high-quality furniture pieces.
- Energy Conservation: Producing new timber involves cutting, transporting, processing, and drying – all energy-intensive processes. Using reclaimed wood bypasses many of these stages, conserving energy.
Wagner Meters has been manufacturing moisture measurement products and services for the wood product industry since 1965 and provides a full range of solutions for lumber producers and secondary wood products manufacturers as well as installers of wood products.
When it comes to measuring wood moisture you want to use the most accurate and reliable moisture meter for wood.
Further Reading:
Wood Production Part II: Manufacturing
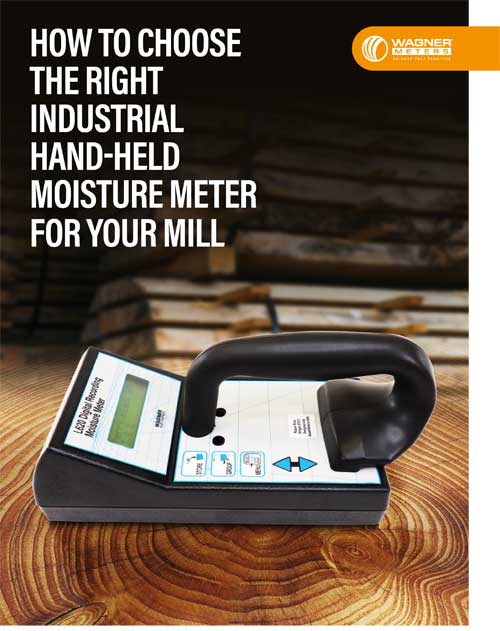
Free Download – How to Choose the Right Industrial Hand-held Moisture Meter for Your Mill
Learn more about Kiln dried wood and why moisture readings are important.
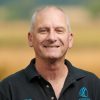
As Sales Manager for Wagner Meters, Ron has more than 35 years of experience with instrumentation and measurement systems in different industries. In previous positions, he has served as Regional Sales Manager, Product and Projects Manager, and Sales Manager for manufacturers involved in measurement instrumentation.
Last updated on February 22nd, 2024
What a beautiful presentation, the actual detailed processes seem to be effective in such a way that they produce quality wood from all sorts of wood types. In addition, a thorough indicator of how we should process and recycle wood.