Brian Boggs Chairmakers: The Art of Building Furniture
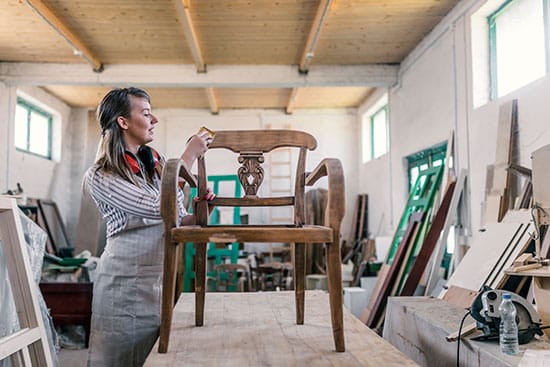
Chairmaking is an intricate process and art form—something that Brian Boggs knows very well. (Note: All pictures on this page are for illustrative purposes. They are not actual pictures from Brian Boggs Chairmakers.)
Brian Boggs is the owner of Brian Boggs Chairmakers, a company out of Asheville, North Carolina, that masterfully designs and builds custom furniture—particularly chairs.
And for Brian, it’s more than just building chairs.
It’s an art form and an opportunity to create pieces that impact how people experience their homes.
“Our chairs are working even when they’re not being sat in,” Brian explains, “because they have a voice in the interior environment.”
We had the privilege of speaking with Brian and hearing his enthusiasm for this work. Keep reading to learn more about his philosophy, process, and advice for furniture makers. We’ll cover:
- How Brian Boggs Chairmakers began
- Brian’s design philosophy
- His chair-making process and the role of moisture
- His top wood choices
- The role of sustainability in his work
- Challenges in the chair-making business
- Brian’s top advice for furniture makers
- The future of Brian Boggs Chairmakers
Chair making allows Brian to create from his imagination and bring to life chairs that not only fulfill their purpose but also delight the people who use them. That creativity has been with Brian all through his life.
Let’s start with how he fostered that creativity and turned it into a business.
How It All Began
Brian has always had a creative bent. At eight, he started taking adult lessons in various art forms—oil painting, sketching, ink, and pottery. He thought for sure he’d become an artist.
Eleven years later, he was in the art department of the library in Lexington, Kentucky, when he stumbled across a book called The Fine Art of Cabinet Making.
“The idea of cabinet making being an art struck me as an oxymoron, so of course, I had to read the book,” he shares. “It opened my eyes to a different world of creative endeavor.”
So, Brian started playing around with some woodworking tools. He didn’t have a workbench, much less a workshop, and grew frustrated because he didn’t have the tools the book’s author had.
But the possibilities remained in the back of his mind.
While working in construction, he ran across another book—Make a Chair from a Tree, by John Alexander. With it, he learned how to build a chair from a log with about $50 worth of hand tools.
Before he knew it, he had requests for chairs and started filling orders. He’s been doing so ever since.
“I loved the sculptural nature of it,” Brian says. For him, it was a vehicle for creativity—a creativity that still impacts his design philosophy.
Brian’s Design Philosophy
Brian believes in combining both creativity and usefulness in the way he designs and builds his chairs:
“I think of the design process and the making process as integrated efforts at taking a tree apart and putting it back together in a more useful form. My job is to make it as useful as possible, as beautiful as possible, and as durable as possible in honor of the tree that had to die to get there.”
For him, usefulness also involves ergonomics. “We experience these pieces with our bodies,” which is why they need to be “comfortable to use and comfortable to be around.”
After all, people don’t keep around uncomfortable chairs! And one of Brian’s goals is to make generational heirlooms that last hundreds of years.
To do so, he veers away from trends and aims for classic designs—ones that won’t fall out of favor after a season. He wants the chairs to appeal to people’s basic sense of beauty and functionality.
“We have been taught through our experiences that the bulk of furniture is not worth much brain power to look at. So, there’s a huge opportunity in my view to stimulate a different experience, and that’s what makes our furniture valuable,” Brian emphasizes. “It’s the people that tune into that, regardless of their bank account, who will value and invest in our furniture.”
Branding also plays a role in the perception of furniture value. By creating a brand that people recognize and prize, he hopes the furniture is less likely to end up in the landfill.
On the more practical side of making chairs that last hundreds of years, Brian knows they have to be able to handle use for that long. Chairs take a lot of stress on their joints, meaning that all the factors—including the joints, the engineering, and the moisture content—must be precise to make them durable.
We’ll learn more about this precision in Brian’s process.
Brian’s Chair-Making Process and the Role of Moisture
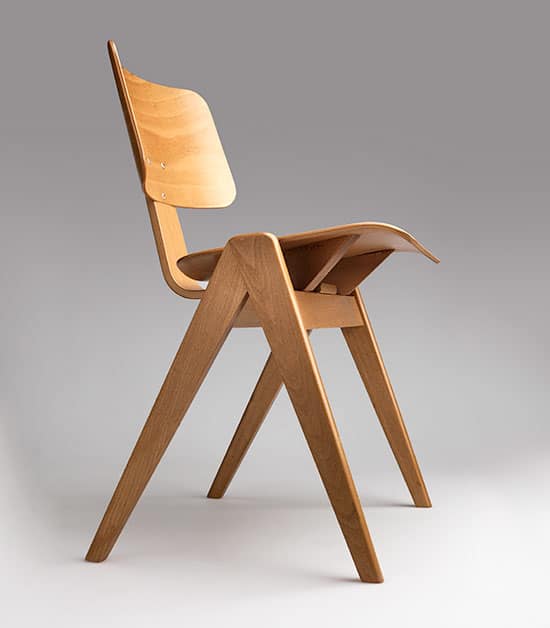
For chairs to effectively handle the weight placed on them, their wood has to be at the right moisture content.
Brian oversees every aspect of the chair-making process and does much of the work himself—from handpicking the wood to cutting the joinery and assembling the chair.
In that process, wood moisture meters play an important role. He uses pinless meters from Wagner Meters (he started 27 years ago with a Wagner L609 and now also has an Orion® 930). He’s found that these meters read “amazingly well” and he uses them to make sure that the wood gets down to about 8% moisture content (MC) before assembly.
Why does MC matter so much?
Brian explains that chairs take a lot more stress than many other types of furniture. For that reason, “everything about how that joint is done is critical.” One little factor that is off could cause failure.
And one of those factors is the wood’s MC.
“If you put a tenon in a mortise, and that tenon was at 10% [moisture content], there’s a strong likelihood that the joint will come loose down the road,” Brian says.
Let’s look at the moisture-testing steps he takes to prevent those failures.
During Drying and Steam Bending
Brian chooses to dry a lot of his wood. He typically allows it to air-dry until it reaches about 12–15% MC.
But before he uses the wood, it may spend some time in storage.
“We use our moisture meters all day, every day, to monitor whatever we’re pulling off the shelf,” he shares. The reason for this is that his woodshop doesn’t have atmospheric control and tends to be high in humidity. If anything has been stacked or stored there for a while, he has to check its moisture levels to determine whether it needs to dry more.
Once Brian is ready to use the wood, he selects his pieces for steam bending. He steam bends the chair legs about 2–4 weeks before doing fine joinery work on them.
Prior to steam bending, he uses a moisture meter to check that the wood is at 10% MC or higher since wood bends easier between 10 and 20% than at an MC below that. For this reason, he doesn’t usually kiln-dry his wood until after the steam bending process. Doing so decreases the risk of a board snapping.
After the chair pieces have been steam bent, he uses a kiln at about 120° F to get the wood down to its final MC.
Before Assembly
Checking the wood’s moisture content is absolutely essential before assembly. Brian aims for about 8%, but it depends on where the product is going. If he plans to ship his product to a drier area, he will sometimes dry the wood to 6 or 7%.
Once the chair is assembled, it’s alright for the MC to increase a little. But the key is to have the wood at its lowest MC during assembly. This precaution ensures that the chair joints remain strong and durable for years to come.
Brian’s Top Wood Choices
Brian Boggs Chairmakers makes custom chairs with the wood species that customers choose. Some of the most popular choices are walnut, cherry, and various types of maple—curly, plain, soft, and hard.
But Brian’s favorites are ash, oak, and hickory.
He’s found that hickory, in particular, is a strong hardwood, allowing him to “make remarkably thin parts that look very elegant without having to worry about structural failures.” That’s not something he can do with woods like cherry or walnut.
Even so, these other woods are appropriate for many of his designs. For example, his Lily chairs require a lot of material, so he’s found it’s best to use lightweight wood to keep the chairs from turning out too heavy.
But species doesn’t matter as much as you’d think.
Brian says it’s “not so much about the species, but about the specific tree.” He’s found that, at times, there’s more variety in trees within one species, such as walnut, than there is between two different species, such as walnut and oak. For this reason, he usually handpicks his wood and looks for walnut that has an elastic character to it, allowing him to design it more freely.
Sustainability also plays a role in the wood Brian selects. More on that next.
The Role of Sustainability at Brian Boggs Chairmakers
To Brian, sustainability involves both responsible management of resources and the making of durable items.
When buying forest-grown wood, he looks for sustainable sources. In addition, he uses urban wood, which is wood from trees that weren’t grown for harvesting but had to be cut down due to death, development, or other reasons.
Brian is conscientious about using mahogany, a rarer wood. He gets much of his mahogany from a non-profit called Greenwood that he helped to start in Honduras.
Greenwood is an artisan training and forest management NGO that helps preserve forests by creating mutually beneficial relationships with villagers and the forests that surround them. That includes craft training and carefully planned micro-scale harvesting of a few trees a year.
In doing this, Greenwood has created a way to support communities economically while protecting forests we all depend on.
But sustainability goes beyond sourcing wood. It also involves using materials responsibly.
“The biggest thing is making stuff that lasts a long time. If you’re buying from the best source, but you’re making stuff that’s only going to last five or ten years, that’s not a sustainable thing no matter where the stuff comes from.”
That’s one reason Brian puts in the detail and effort to be sure his chairs last, in his words, “basically forever.”
Doing so is not without its challenges, though.
Challenges in the Chair-Making Business
Brian’s biggest challenges over the years have been sourcing quality wood and finding employees.
Often, when he would get wood from a supplier, the wood would be wet, damaged, or different in quality or character than he specified
That’s why he has chosen to process most of his wood on-site. The downside is that wood processing takes away from the time he would like to spend on design and other parts of the chair-making process.
However, he believes this situation might change since he recently discovered a quality supplier.
The COVID pandemic in the past few years made it difficult for him to source wood, too. For example, he couldn’t find curly maple for 18 months!
Since he’s had so many problems with sourcing, he has opted to overbuy wood when he does find it so that his inventory doesn’t get too low. Of course, that has its challenges, such as needing more storage space!
Another residue of the pandemic is the challenge of getting employees. Brian has found that few people are trained to make the type of furniture he makes.
Despite these challenges, he feels privileged to have worked as a furniture and chair maker for the past 41 years. And he offers some excellent advice for those just starting.
Brian’s Top Advice for Furniture Makers
Just like any other profession, furniture making involves understanding the business, watching your overhead, and making sure you’re selling enough to cover costs. But one of the biggest things Brian has learned over the years is the importance of “knowing your why”—the reason you do what you do.
That reason is what will guide every aspect of your work as a furniture maker, such as what furniture you’re going to build and how you’re going to market it.
Brian points out that custom furniture making is less lucrative than many other manufacturing opportunities, especially with all the inexpensive furniture on the market these days.
To make it in the furniture business, you have to understand the value and importance of handcrafted furniture. Otherwise, “it’s going to be hard to convince people why they should invest in you and your work.”
And becoming successful, especially in chair making, takes time. It takes a while to learn your way in the design, production, and marketing of this product.
Thus, having a clear why is what will sustain you—and it’s what has sustained Brian in his craft for many years.
The Future of Brian Boggs Chairmakers
Brian’s business celebrated its 40th anniversary this year (2023), and he is excited about upcoming projects: “We’re looking to collaborate more with outside manufacturers with new designs.”
Up until now, his small manufacturing capacity hasn’t been able to support a broader portfolio, so he hasn’t been able to put out a lot of new designs.
But he’s hoping to change that.
He’s currently working on an outdoor line and also envisions other chair designs, such as hospitality furniture.
Truly, Brian’s love for this work shines out, and to him, the most rewarding aspect is crafting items that appeal to people’s values and sense of beauty.
As he looks ahead, he’s enthusiastic about continuing to stimulate that love for beautiful wooden pieces. To learn more about his work and be inspired yourself, visit BrianBoggsChairmakers.com.
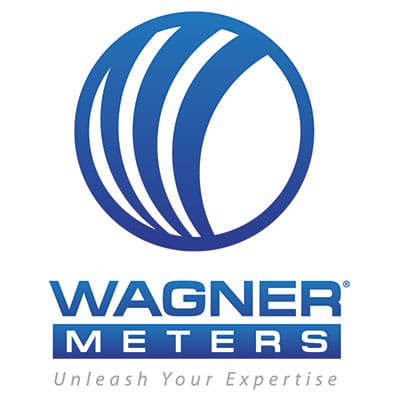
Wagner Meters is a family-owned American business that aims to provide solutions in moisture measurement technology that will enhance the quality and value of each customer’s project. With an almost 60-year legacy of innovation, Wagner continues to be a resource for both individual craftsmen and high-performance commercial endeavors.
Last updated on March 13th, 2025