History of Wood Moisture Meters
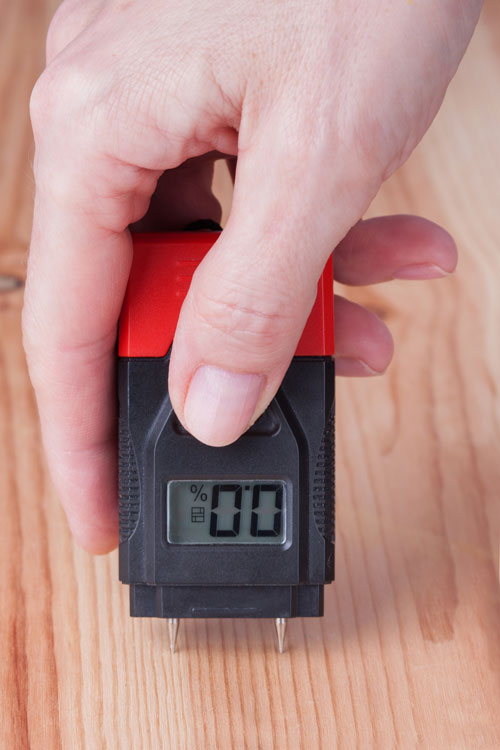
Pin-type wood moisture meter
Even before the science of woodâs relationship with moisture was well-understood, woodworkers had to factor in how moisture would affect their materials.
Fortunately, we understand well the hygroscopic properties of wood today. Thus, we’ve been able to use that knowledge to design wood moisture meters that can provide us with quantifiable data about a piece of woodâs moisture condition. As our collective understanding has advanced, the testing methods have evolved as well.
Today, there are two main types of hand-held wood moisture meters: pin and pinless. Each relies on different electrical properties that are impacted by the amount of moisture held in the wood being measured, which weâll explore in detail later in this article.
For now, itâs enough to say that pin-type meters use two nail-like electrodes that get inserted into the wood and measure the current that flows between them. Pinless meters use sensor plates that lay flat on the woodâs surface and measure the behavior of an electric wave they send through the wood.
Without getting into the science of each moisture meter type, the most apparent differences between them are what they do to the wood being measured, and how easy they are to use.
Pin meters leave holes in the wood being measured. This makes them useful for evaluating the moisture content of firewood or pieces of wood where leaving multiple holes wonât negatively impact the structural integrity or aesthetics of the final product.
In contrast, pinless meters donât leave any physical markers behind. They can only be used on flat wood and the entire plane of the sensor needs to maintain contact with the wood during a reading.
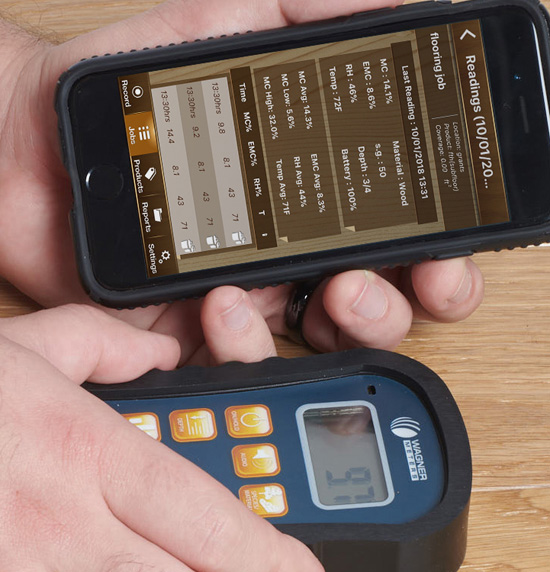
Orion 950 Smart Pinless Wood Moisture Meter
A slow pace of work measuring woodâs moisture content is another outcome of having to insert or hammer in pins when using a pin meter. Inserting the pins to the right depth, removing them, and ensuring the pins remain in good condition to take a reading takes time.
Consequently, when having to assess the moisture condition of a large piece or large batch of wood, you have to invest a significant amount of time. The more likely scenario is that you’ll simply take fewer readings. One extends project timelines and costs, while the other means youâll be making decisions with fewer data points guiding you.
You can work much more efficiently with pinless meters since they require less physical effort to use and aren’t as vulnerable to physical damage as the pin electrodes.
But this is where we are today. Electric moisture meters have nearly a 100-year history. Interestingly, they also still rely on an even older method â oven drying â to validate their accuracy. To appreciate how hand-held wood moisture meters of today operate, itâs worth digging into the evolution of the technology on which they rely.
Oven-Dry Methods Are the Gold Standard for Measuring Wood Moisture
The earliest method used to dry wood is air drying or “weather drying.” That takes time. Wood would often be left for years before being used. Early attempts to speed up the drying process resulted in various types of âdry-housesâ being built. These were simple structures set over dugout cellars holding a brick or tile furnace.
In the United States, the use of âdry-housesâ wasnât the norm, in part because they presented enormous fire risk. There was some experimentation using steam pipes in the 1850s, but it didnât go well. Eventually, the first successful wood drying kilns, drying chambers that had some thermal insulation, were popping up around the Midwest in the 1870s.
Through trial and error, kiln operators discovered that drying wood at lower temperatures with circulating air produced better results than turning the heat on high. Eventually, the trial and error approach by businesses seeking to minimize drying times while maximizing outputs got assistance from the scientists and researchers. Through scientific inquiry, researchers began discovering and validating a wide range of physical properties of wood. Some of their discoveries included understanding the cellular structure and chemical properties of wood.
In turn, this led to understanding how physical differences among wood species, and even among the same species grown in different locations, impact the drying process of the wood.
Through the rise of wood research, wood scientists developed a formula for specifying the moisture content of a piece of wood as a function of its weight and expressed as a percentage.
Moisture content (MC) = (Starting weight – oven-dry weight)/ oven-dry weight * 100
As such, the oven-dry method provides a direct measurement of a piece of woodâs moisture content. If you have a wood-drying oven, you can weigh the wood both before and after itâs run through a drying cycle in the oven. ASTM D4442 (standard test method for direct moisture content measurement of wood and wood-based materials) states that oven-drying provides âthe highest accuracy or degree of precisionâ and is âthe reference (primary) standard for determining the moisture content of wood and wood-based materials.â
As a result, oven drying wood in compliance with ASTM D4442 is used as the reference point for calibrating hand-held moisture meters per ASTM D4444 (standard test method for laboratory standardization and calibration of hand-held moisture meters).
Hand-held moisture meters provide an indirect measure of moisture. Since water conducts electricity, the hand-held meters collect data about the behavior of electric currents or waves in a piece of wood. This data is then used, along with other relevant data points, to calculate the woodâs moisture content.
Evolution of Electric Wood Moisture Meters
Humanity has long understood that wood contains moisture; that it dries out and can reabsorb moisture when in contact with water. In truth, scientists have also known about the relationship between water and electricity from nearly the moment electricity was discovered. Specifically, they knew that water conducts electricity, even if the specific chemical process that occurs in water as it allows electrical charges to pass through it has been more recently documented.
Researchers first validated the idea that we could use the electrical properties of wood as a measure of its moisture content in the late 1920s. One of the first portable electric wood moisture meters that we find documentation for, is a âblinker-typeâ meter, in 1927. This meter had a neon lamp attached to a capacitor, which was in contact with the wood. The capacitor would absorb the charge running through the wood. When the capacitor was fully charged, the neon lamp would briefly light up. The faster the capacitor could recharge, the faster the lamp would blink.
How quickly the capacitor could recharge was a function of how much resistance was in the wood. Since moisture conducts electricity, the more moisture in the wood, the faster the capacitor would reach a full charge. If there were high resistance in the wood (i.e., low moisture), then the lamp would blink slowly.
Within the following ten years, a new type of electric moisture meter was developed: a vacuum tube meter. This meter used a vacuum tube voltmeter as part of a Wheatstone bridge circuit, which uses a resistor to measure against the wood being measured. The vacuum tube meter is the direct precursor to the resistance moisture meters used today.
By the mid-1940s, pin-type meters were commercially available. They worked (and still do) by measuring the flow of an electric current between probes inserted into the wood. Like the early blinker-type meter, the more the current traveled between probes was an indicator of lower moisture levels.
Without the conductivity of high levels of moisture, the dry wood presented resistance that nearly eliminated the currentâs flow. Some early pin meters used four probes. Modern pin type moisture meters require only two probes.
During this period when resistance meters were hitting the market, researchers were also exploring how dielectric properties could be used to measure moisture in wood. Dielectric materials can transmit electric currents without being conductors themselves. This research ultimately resulted in two other types of wood moisture testing methods that work on two different dielectric principles.
Without diving too deeply into electrical engineering, these two types of dielectric meters used radio waves to measure moisture levels. The power-loss type of meter looks at how much electromagnetic energy is lost, which correlates to moisture levels. The capacitance moisture meter takes the opposite approach. It looks at how much electrical energy can be stored. What they have in common, on a practical level, is that neither requires pins to break through the woodâs surface.
Instead, they use sensor plates that emit a radio frequency through the wood. The Forest Products Laboratory (FPL) of the U.S. Department of Agriculture had developed a capacitance-type machine to measure wood moisture levels, but it wasnât commercially available. By this time, many manufacturers were selling pin-style moisture meters.
The Modern Era of Electric Wood Moisture Meters
By the early 1960s, there was one common power-loss type moisture meter on the market. During this period, Delmer Wagner, the founder of Wagner Meters, was working as an electrician for a sawmill in Oregon. The mill used a large, unwieldy vacuum-tube in-line moisture detector.
To build a moisture meter that was both smaller and easier to calibrate, Delmer designed the first in-line moisture meter. This in-line moisture measurement system used transistors to measure moisture. Delmer eventually left the sawmill and, in 1965, founded Wagner Electronics (known today as Wagner Meters), which built in-line moisture meters for the lumber industry.
Nearly all handheld wood moisture meters on the market through the late 1980s were pin moisture meters. However, these new pinless moisture meters were still quite large, hard to calibrate, and too sensitive to ambient conditions. Consequently, the pin moisture meter market thrived, while there were very few pinless meters.
In the 1990s, Wagner Meters set out to develop a pinless wood moisture meter that resolved the shortcomings of the pinless meters then on being sold in the marketplace. Wagner Metersâ first line of hand-held pinless moisture meters had an improved circuitry using electromagnetic waves that resulted in more accurate moisture readings.
In addition, the circuitry was less sensitive to ambient and wood temperature. Wagner Meters was also able to reduce the size of the hand-held meter significantly from what was currently available on the market. Pinless meters from other manufacturers generally weighed at least 10 pounds. The original moisture meters were designed for sawmills, but Wagner Meters added one explicitly designed for woodworkers by the mid-1990s.
The original line of Wagner pinless moisture meters was analog. The analog line was replaced by a line of digital pinless moisture meters in the early 2000s. These meters used microprocessors, so the size of the Wagner hand-held meter continued to shrink. By this time, numerous studies had validated that Wagner pinless meters delivered more accurate readings than pin moisture meters.
These studies are significant because they debunked the widespread assumption that pin meters were more accurate than a pinless meter. The fundamental technologies used in both pin-style and pinless meters remain unchanged. Today, most advances in wood moisture meters are focused on the value-added features embedded in the meters and related services.
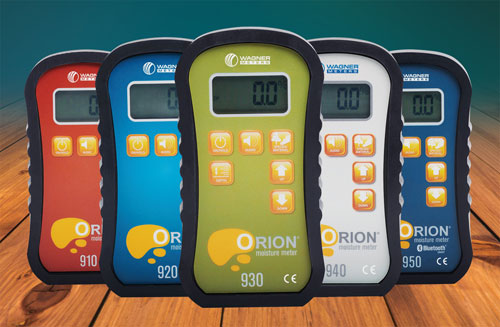
The Orion line of digital pinless wood moisture meters.
As a result, Wagnerâs newest line of wood moisture meters, the OrionÂŽ, includes new, sophisticated features that make woodworkersâ lives easier.
For example, the Orion meters are the only ones in the market that can be calibrated on-site using the On-Demand Calibrator sent with each Orion meter. All other hand-held meters need to get sent to the manufacturer for factory calibration, which costs time and money.
Some of the most useful value-added features improve the meterâs data collection and management. Since knowing the point of equilibrium of moisture content (EMC) of the in-use location is so vital to protecting wood from future moisture-related damages, the Orion 950 functionality includes calculating the EMC for users.
The pinless meter collects an ambient temperature and relative humidity reading which it uses to calculate EMC. That EMC can then be used as the âtarget moisture contentâ for the project youâre working on, or be used to predict drying patterns. Moisture meter-based EMC calculations relieve users of the hassle and uncertainty of calculating EMC themselves.
Pinless Meters Prove More Accurate and Reliable than Pin-type Moisture Meters
While pin and pinless moisture meters both work on how electric properties work on wood, they each are looking at different properties. Simply put, pin meters react to a wood’s chemical properties, and pinless meters respond to the wood’s specific gravity.
Both a piece of wood’s chemical makeup and density vary by wood species. This is the reason why both meters require adjustment for the species being measured to get an accurate moisture reading.
According to the FPL, some of the issues that impact the accuracy of a meter reading are weather conditions, electrode contact, wood temperature, and the skill of the operator. Many of these issues affect pin type moisture meters more readily than they do pinless meters. Studies have shown that pinless meters are often more accurate and reliable than resistance meters.
For instance, pin meters are highly sensitive to wood temperatures, which can interfere with getting an accurate reading. If the air temperature is far off that mark in either direction, the operator has to adjust the meter readings based on the exact air temperature where they were taken.
Making wood temperature adjustments is only one way where the subjective skill of the meter operator can impact a pin meterâs accuracy. Pin meters also require precise operator skill to ensure both electrodes are correctly driven into the wood and to the right depth. Without proper alignment or depth, the electrodes may not measure moisture accurately for that spotâs moisture level.
The most critical operator skill in placing a pinless moisture meter is simply to ensure that the sensor plates lay flat on the woodâs surface.
For this reason, pinless meters arenât typically usable on firewood. Otherwise, the pin meterâs fast and easy user experience means that woodworkers usually take more readings with it than with pinless meters. Having more moisture level data provides a more accurate picture of a batch of woodâs moisture condition.
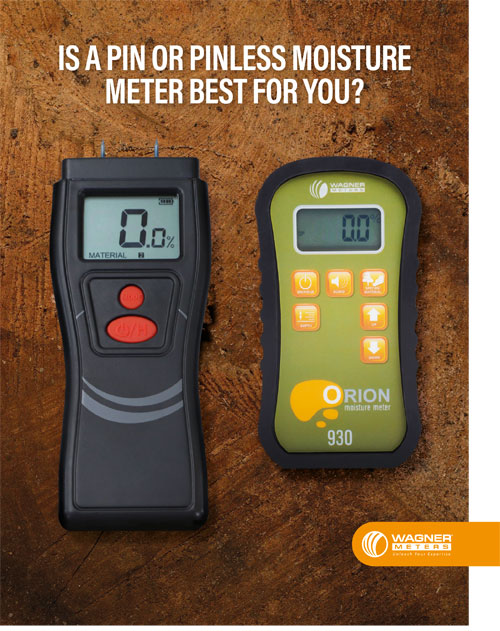
Free Download – Is a Pin or Pinless Moisture Meter Best For You?
The History of Wood Moisture Meters: From Trial and Error to an Essential Woodworking Tool
As the lumber industry grew apace with the industrial revolution during the 19th century, itâs logical that lumber mills sought ways to speed up the drying process in ways that didnât destroy the wood. Their trial and error methodology, along with their anecdotal knowledge of weather drying, helped them innovate.
They realized how circulating air helped maximize outputs by allowing for lower temperatures to be used to dry lumber. They saw how different wood species reacted under similar circumstances. Their practical explorations were the foundation of formalized wood science.
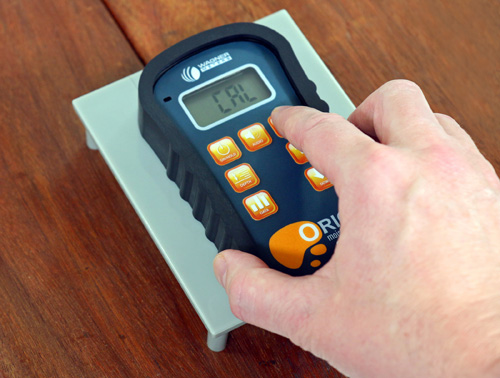
Orion meters from Wagner Meters are the only pinless wood moisture meters available that can be truly calibrated in the field instead of being sent back to the factory for recalibration.
Through the rigors of scientific and academic inquiry, our understanding of woodâs physical and mechanical properties expanded significantly throughout the 20th century. Through this research, the industry has been able to specify how moisture moves through wood and how excessive moisture negatively affects wood.
Coming full circle, the lumber industry has used wood science contributions to develop the tools needed to measure the moisture content of wood, both directly and indirectly, with a high degree of accuracy.
As wood science revealed more about the interplay of moisture and electricity within the wood, meter manufacturers used these advances to design and build commercially viable moisture metersâthe hand-held moisture meter in particular.
With reliable and accurate hand-held wood moisture meters, every woodworker, from the operator of a lumber mill to the weekend hobbyist, has the ability to make informed decisions about when wood is ready to take the next step in its journey towards its intended use. As such a powerful tool, wood moisture meters are now a staple for almost all woodworkers, which only begs the question of why they arenât used by all woodworkers.
Indeed, now that anyone can access accurate moisture condition information about wood through a hand-held moisture meter, they have a responsibility to do so.
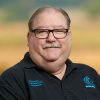
Tony Morgan is a senior technician for Wagner Meters, where he serves on a team for product testing, development, and also customer service and training for moisture measurement products. Along with 19 years field experience for a number of electronics companies, Tony holds a B.A. in Management and his AAS in Electronics Technology.
Last updated on January 10th, 2025