The Lumber Price Roller Coaster – How to Ride it Safely
Are the wild ups and downs of lumber prices making your construction or DIY projects feel impossible to plan? Youāre not alone. The good news is that while you canāt control the market, you can protect your projectsāand your budgetāfrom costly mistakes.
In this article, weāll break down exactly why lumber prices have been on such a roller coaster and, more importantly, what you can do to keep your projects on track.
Youāll learn:
- Why lumber prices keep spiking and dipping (and why this isnāt ending anytime soon)
- Practical strategies to focus on what you can controlālike proper wood acclimation
- How an accurate moisture meter can save you from rework and costly project delays
- Expert insights on whether lumber prices will stabilize soonāor keep everyone guessing
Ready to ride the lumber price roller coaster without getting derailed? Letās dive in and discover the simple steps that can protect your projects, profits, and peace of mind.
Table of Contents
- Why Lumber Prices Have Been Going Crazy
- Focus on Controlling What You Can Control
- Accurate Information Breeds Confidence
- Will Lumber Prices Stabilize Soon?
For decades, lumber prices stayed within $300 to $500 per thousand board feet. Since the pandemic, however, lumber prices have been on a roller coaster.
Experts first thought lumber prices would plummet during the pandemic. Instead, they skyrocketed. They started creeping up in November 2020 and hit their high of over $1500 per thousand board feet in May 2021.
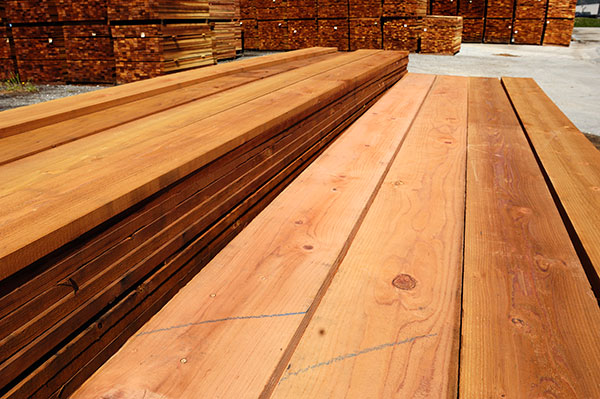
Many of the factors contributing to the recent roller coaster in lumber prices remain unchanged
But that high was short-lived. According to the National Home Builders Association (NHBA), framing lumber prices in late August 2021 are back at $400.
Don’t get comfortable, however. This ride isn’t over yet. Many factors that caused the initial spike and drop havenāt changed.
Why Lumber Prices Have Been Going Crazy
The lumber supply dropped when the pandemic and lockdowns first hit in March 2020. The popular assumption was that housing construction and renovations would stop. Sawmills and manufacturers closed down or greatly restricted operations. Suppliers liquidated inventory.
The popular assumption was way off the mark. Demand for lumber jumped. Consumer demand spiked. People stuck at home started catching up on their home improvement projects. Many also discovered new projects to accommodate everyone working and attending school from home. Those backyard offices had to get built somehow.
Restaurants and bars started building “temporary” outdoor seating and dining areas. Residential housing construction also spiked. Housing starts in the United States increased by more than 50% between May 2020 and May 2021.
The surge of federal stimulus programs and low mortgage rates set up the classic formula for price inflation: too many dollars chasing too little supply.
May 2021 was the lumber price high point, after which it took a sharp downturn. Skyrocketing prices halted consumer home projects. Construction slowed down partly due to materials and worker shortages but also due to the inability to predict costs.
As lumber prices have plummeted, some demand has returned, yet supply concerns remain. Wildfires in the United States and Canada are impacting the lumber supply. Concerns about a fall/winter Covid resurgence affect worker availability and workplace safety.
Itās no wonder that builder confidence has dropped from the post-Covid boom back to pre-Covid levels. According to the NAHB/Wells Fargo Housing Marketing Index, builder confidence in March 2020 was 72, hit 90 by November 2020, and is back at 75 in August 2021.
The number of housing starts and permits also presents a mixed picture. Housing starts were down in July 2021, but housing permits went up.
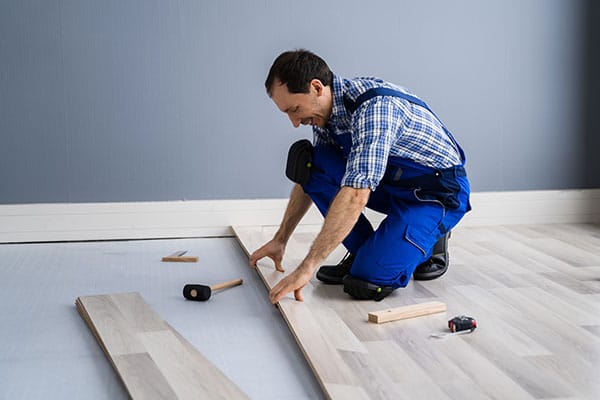
While you canāt control the price of materials, you can control whether your wood is fully acclimated to service conditions before you use it for your project.
The bottom line is that the lumber market will remain unpredictable.
Focus on Controlling What You Can Control
The lumber market roller coaster has affected all its related markets, like plywood and engineered wood. With unpredictable prices and supply, your project budgets have never been harder to manage. And you certainly donāt want remediation costs for addressing moisture-related damage to threaten your bottom line, especially when wood prices could quickly spike.
You can’t control material prices, but you can control whether the wood you’re working with has fully acclimated. Installing wood flooring that hasn’t acclimated to its service conditions increases the risk of a moisture-related failure.
You can’t guess a wood’s moisture content. Letting it sit for a few days in the service location is no guarantee that the wood’s moisture content is acceptable.
The only way to know the wood’s moisture content is to measure it with an accurate wood moisture meter. There are too many variables that impact wood’s moisture content. The wood species, the ambient conditions at the in-service location, and the manufacturer’s drying process – all impact moisture content. Not using a wood moisture meter leaves you relying on guesswork.
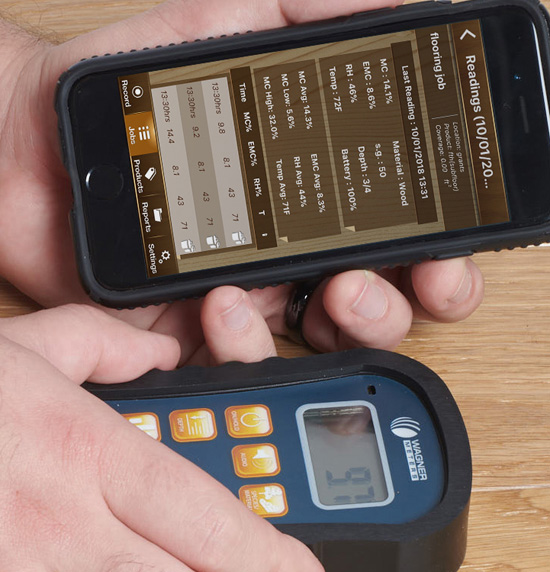
Eliminate moisture-related problems by using a moisture meter to measure the moisture content of your wood.
Accurate Information Breeds Confidence
There’s another consequence to the lumber price and supply unpredictability. It raises the financial and operational costs of redoing a project.
If you need more wood to complete the remediation, will you be able to get it or afford it? If supply is low, will using your inventory for a remediation project impact your ability to complete a new project?
The alternative is to eliminate the risk of flooring failure by using a moisture meter to measure the wood’s moisture content. Manufacturers specify the acceptable MC range for their products based on their internal testing. They know what MC range each particular product can handle.
Measuring the wood MC content with a moisture meter will give you the confidence to know when the wood is in the appropriate range based on manufacturer testing.
Taking moisture content readings throughout the acclimation process helps you take control of your project timeline. If you see it’s not drying fast enough, you can take steps to speed that up. If it’s drying faster than expected, you can get ahead on your timeline. Either way, tracking the wood’s MC with a moisture meter is knowledge, and knowledge is confidence.
If you want to learn more about acclimating wood, check out this article check out this article.
Will Lumber Prices Stabilize Soon?
Who knows if lumber prices will stabilize soon? The market was wrong with its early pandemic predictions. The futures market went up in August 2021, but itās back within the pre-pandemic range (the top of the pre-pandemic range).
Will it stay there? Is this the point of stabilization? Iām not an economist, but I think itās not. There are too many mixed signals and unpredictable variables. Even if prices do stabilize soon, thereās good reason to think theyāll settle at a higher than the pre-pandemic range. The impact of lumber prices on your project costs and profit margin isnāt going away.
Donāt waste time and money redoing projects because you installed wood that didnāt fully acclimate as needed to its in-service location. A quality wood moisture meter is easy to use and indispensable to ensuring your projects donāt fail.
Protect your projects from moisture-related failures with Orion moisture meters. These highly accurate, easy-to-use devices can help you confidently measure the moisture content of your wood, ensuring successful installations every time. Get your Orion moisture meter today and take control of your project outcomes!
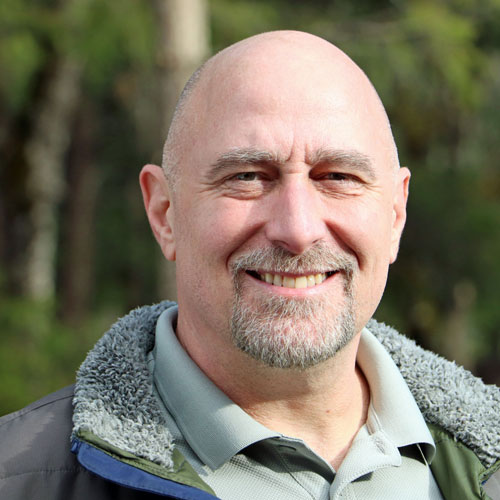
Jason Wright, Business Development Specialist for New Products, joined Wagner Meters in 2019. He comes to Wagner with over 35 years of experience in the flooring industry.
Last updated on March 17th, 2025