Oregon Woodturner Harvey Bower Gives Advice to Beginners
Just as an artist brings a canvas alive with his bold use of colors and hues, so too does Harvey Bower bring blocks of wood alive, transforming them into decorative forms and shapes with skilled turns of a lathe.
Bower is a professional woodturner living in the historic gold rush town of Jacksonville, Oregon, nestled in a fertile valley beneath the Siskiyou Mountains. He works in a small converted garage that was once a dentistâs office.
He coaxes beauty out of wood and often presents the townsfolk with his creationsâfrom burial urns to spindles for stair railings to commemorative gavels. Heâs a giving man who uses his skill to help restore the townâs antique homes, provide elegant objects for the townâs fund-raising auctions, and donates ornamental vessels to college galleries.
The magic begins in Bowerâs shop, a model of efficiency and functionality. Every bit of space is used. Tools adorn the walls. Wood chunks, finishing supplies, waxes, and oils fill the cabinets. A lathe and other pieces of equipment occupy the floor. Even the rafters hold stacks of wood.
âThink of a single car garage, something that would fit a Model T. Then cut the length in half. Thatâs the size of my woodturning shop. The other half is used for storing wood,â Bower says.
âBecause itâs such a small area, everything I need is within reaching distance. I can turn around and pick the tools right off the wall. So I donât have to walk across a big room to change tools.â
âWhen youâre turning, youâre forever changing tools. You may have 10 seconds on this one before you switch to another that works better. Iâm constantly switching tools back and forth all the time. If a tool is too far away and you donât grab it, then you start to make do. And thatâs not good,â he explains.
Bowerâs creations grow out of his fascination for woodâthe way it feels, the sweet aroma after itâs freshly cut, the warmth and wild beauty of its colors. Although he once worked as a wood carver, he switched to woodturning as he found the turning process immediate and richly satisfying.
âNothing Beats a Good Tool.â
Bower will be the first to tell you that to be successful at woodturning you must first possess a passion and deep appreciation for wood. Thatâs paramount. Next, you must master basic woodturning skills. That comes with practice and patience. And finally, you must have the proper tools.
âNothing beats a good tool,â he declares.
So Bower buys custom tools made from the highest grade steel. Most come from Englandâcompanies like Crown, Hamlet, and Robert Sorby. Others he buys from Thompson Lathe Tools in the United States.
âIâm an old metallurgist. When I see a diamond checker on the end of the tool to see what the hardness is, I know itâs a quality tool. If you want something thatâs going to do the best job, it has to be the right steel,â he asserts.
It takes a variety of tools to sculpt wood in a lathe. A beginner may be tempted to buy a basic starter kit. Bower emphatically says, âNo! Because itâs somebody elseâs concept of what your ability is. Youâll likely end up with tools youâll never use and so waste your money.â
He says beginners can start with a few basic lathe tools to get started. He recommends:
- Spindle roughing gouge â ž-inch
- Spindle gouge with fingernail profile â 3/8-inch
- Curved scraper â ž-inch
- Round nose scraper â ž-inch or 1-inch
- Parting tool â 1/8-inch
- Bowl gouge â ž-inch (if theyâre going to do bowls)
All these tools come in a wide variety of sizes and shapes, so a beginner can buy more tools as the skill and need increass. Another tool that should be included, but later, is the skew chisel. Itâs the most difficult tool to learn to use and sharpen, but one that has many virtues once mastered.
Mini-Lathe, Micrometers and More
All of these tools are used with a lathe. Because of his shop size, Bower uses a mini-lathe with an 18-inch bed instead of a larger lathe with a longer run. The mini-lathe, ideal for creating smaller objects, turns a spindle up to 18-inches long and 12-inches in diameter.
Although he uses a smaller lathe, he insists that it come with the most powerful motor one can get for that size. He also highly recommends having a speed control. It eliminates the need to change the belt to a different pulley size every time a change in speed is needed.
âTo change the speed on an inexpensive lathe you have to move the belt to the proper pulley size in order to get just one speed setting. So an electronic speed control, which gives you an almost endless choice of speeds without the hassle, is pretty important,â he says.
âIt must also be able to turn in both directions. This allows me to cut in one direction and sand in another. You want to sand the wood in the opposite direction because you donât want debris spraying into your face. You want it going into a vacuum system, which is a lot safer,â Bower notes.
Although he owns a drill press, he says 90 percent of his drilling is done with the lathe. A woodturner also needs a band saw, a small Gentleman’s saw to do final cutoff, and a chainsaw for cutting logs and larger pieces of wood.
Because measurement is critical in woodturning, Bower uses micrometers and calipers. For example, if he wants a lid to fit perfectly on a wooden vessel, heâll use a micrometer. Micrometers are used for measuring diameters, while calipers measure inside and outside diameters as well as depth.
Bower sharpens his tools every five minutes or so to keep them from grabbing or gouging the wood being turned. âIf the wood is turning about 2000 rpm, thatâs like sticking your foot out a car door while going down the road at 60 mph. Think of the abrasive action; it doesn’t take long for the tool to get dull,â he says.
For sharpening, he uses an 8-inch slow speed bench grinder with sharpening jigs that enable him to get the correct angle on each tool. âBecause the jigs are very precise, I donât have to guess about the angle. I can sharpen my tools at the same angle every time,â he adds.
Checking Moisture Is Critical
A moisture meter is another essential tool Bower keeps handy. âYou really need to use a moisture meter,â he says.
âSome of the wood I use is very expensiveâanywhere from $100 for a small piece and up. I have one piece thatâs $900. When you spend that kind of money on wood, you donât want to turn it with the wrong moisture content in it. It can crack or shrink. Thatâs why I use a moisture meterâto prevent that from happening,â he confides.
âWhen I cut a top to fit perfectly on a vessel, if I donât check the moisture content, either it wonât fit next week or it will bind up so tight that it will never work. Or, if I use poplar wood for staircase spindles, it has to be checked for moisture because itâs a soft wood and contains more moisture than a hardwood. It also has to stabilize in your environment. You canât store it somewhere else and then bring it in and think youâre going to work on it because it will swell or crack. Thatâs why itâs critical to check for moisture,â he says.
Bower works with many different woods, including black cherry, maple, figured maple, any fruit wood, pecan wood, tulipwood from Brazil, and jet black ebony from Africa. Each species has a different moisture content (MC) level, so a woodturner needs to know the MC of each species being used. For example, maple is going to have different MC levels than hard oak or ash.
He appreciates Wagner Meters because the company produces a variety of moisture meters for wood for every situation. The OrionÂŽ moisture meter line from Wagner Meters measures the MC for common hardwoods, softwoods, and exotic species. With its programmable fast selection species settings range, each wood species can successfully be measured for its MC.
Another thing he likes about the Wagner meters is that they are pinless, meaning they donât put unsightly holes in the wood surface. âIf youâre testing a board that you just finished planing, you donât want to stick pins into it. You want a pinless meter. Theyâre probably the best meters for any operation because they cover the spectrum,â Bower says.
âIf you invest the time, effort, and money into your work, itâs just good economics to use a moisture meter,â he adds.
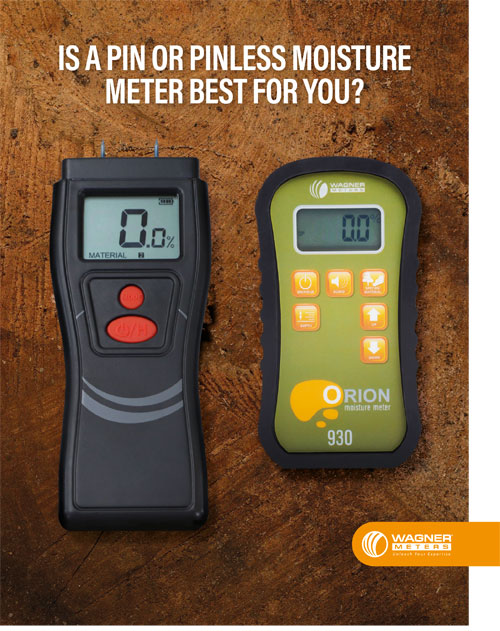
Free Download – Is a Pin or Pinless Moisture Meter Best For You?
Be Safe and Comfortable
Safety and comfort are other important factors when operating a woodturning shop. Bower takes both seriously.
Among the things heâs done to be safe and comfortable is install ample lighting, including a high-intensity LED light. âWhen I throw the lights on, it looks like the landing craft of ETâs spaceship. But you need to see what youâre doing to prevent costly mistakes and prevent accidents,â he remarks.
Since his shop is on concrete, he installed a thick wood platform using industrial plywood to avoid standing on the hard concrete floor and to prevent slipping. It also gives him a height advantage relative to the lathe.
In the winter, he uses a large parabolic electric heater and has infrared heat lamps installed on the ceiling directly above the lathe. The infrared lamps help keep his hands warm and flexible.
To manage the dust, Bower uses a vacuum system containing two different types of filters. It sits on the side of the lathe. He also uses a face mask for the dust and for those woods that may cause an allergic reaction.
âSome people donât realize that certain woods are highly toxic. It can be like turning a poison ivy branch. So breathing toxic wood is not good. Once I worked on some rosewood from either Indonesia or India. The next morning I woke up with a rash from head to toe,â he says.
Now Bower checks woods online for their toxicity and has become quite knowledgeable about which woods are harmful. He also uses a book called Wood for Woodturners, by Mark Baker, which lists wood toxicity.
Occasionally, he uses a face shield if he works on wood thatâs potentially explosive. And to address shop noise, he has insulation in the ceiling and walls, and wears earplugs when using any loud equipment.
The Best Tools Are Worth the Investment
A good woodturner treasures the value of wood, so he uses the best toolsâbe it a tool to cut, measure, or monitor moisture levelsâto create beautifully-crafted art.
âHaving the best tools makes all the difference in producing quality work. They are a pleasure to use and are well worth the extra money. They are easier to use and harder to abuse than cheaper, inferior tools. Theyâll repay your investment in no time,â Bower says.
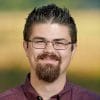
Eric is excited to fight the moisture problems that cause billions of dollars of waste in the United States and the rest of the world. It also helps that he enjoys spending his free time woodworking, and he knows his projects will be free of moisture issues.
Last updated on May 4th, 2021